Three dimensional detection scheme for super large forgings
In the manufacturing process of the super large forging parts, the technical parameters and the performance index are very high. The forging process is very complicated, the precision requirement is high, the forging process is very difficult. A domestic heavy equipment manufacturing enterprises want to super large forgings produced were analyzed using Huaguang 3D scanner, and detected data report, product improvement needs.
Practical problems
1 because of the large size of the super large forging parts, the traditional measuring equipment can not be measured and make a written test report, the measurement is very difficult.
2 super large forging of large volume, 10 meters in diameter, large pieces of this 3D scanner must use large format scanning, the use of other 3D scanner, scanning time, low precision, large amount of data, the scanning scanning data was unable to complete mosaic.
CO3D solutions
The heavy equipment manufacturing enterprises are very high requirements for super large forging production, in order to solve the large forging detection problem, the heavy equipment manufacturing enterprises linked to Huaguang 3D, hope to be able to solve the difficult problem of detection, and 3D scanner speed and precision to ensure the completion of the work of scanning the needs of its customers under the.
1, the preparatory work
Spray imaging agent: improving the sample surface color contrast scan data to obtain better.
Marking point: the data obtained in the scanning software to carry out the positioning and splicing.
Point to point: make the 3D photogrammetry system to obtain the 3D coordinates of the object surface.
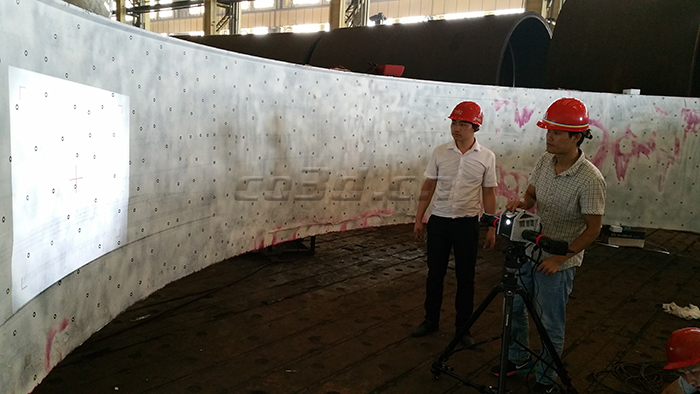
Super large forging work site
2, 3D Photogrammetry
Huaguang engineers use 3D Photogrammetry System for super large forging surface 3D coordinates, using 3D photogrammetric system (HL-3DP) to take a few pictures of nuclear forgings, through 3D measurement, HOLON3DP software will automatically combine these images after operation, 3D coordinates can be obtained for each encoding point center. Calculate the 3D coordinates of the object surface of the key point of information value.
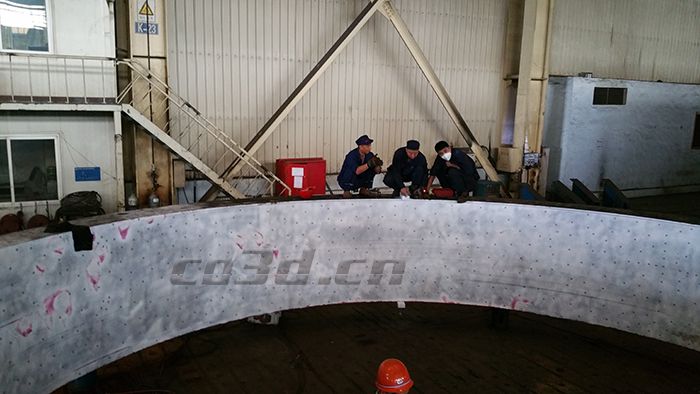
Diameter of about 10 meters, 2 meters high and super large forgings
3, three-dimensional scanning
The 3D coordinate data of the super large forgings were imported into the HOLON3DS scanning system, and the 3D scanner was used to obtain the 3D data of the super large forgings by using the 3D scanner alpha 7000. The 3D scanner with a large scanning area, scanning speed and high stability characteristics of equipment. Using 3D photogrammetric system (HL-3DP) and 3D scanner with alpha 7000 can point cloud information on a large area of the surface correction, significantly improve the overall accuracy of 3D scanner point cloud, improve work efficiency. It only takes 2 hours to get the 3D data of the nuclear forging parts, and compares the original data of the super large forgings with the 3D scan data to obtain the test report.

Diameter of about 10 meters, 2 meters high and super large forgings

Three dimensional inspection of super large forging parts
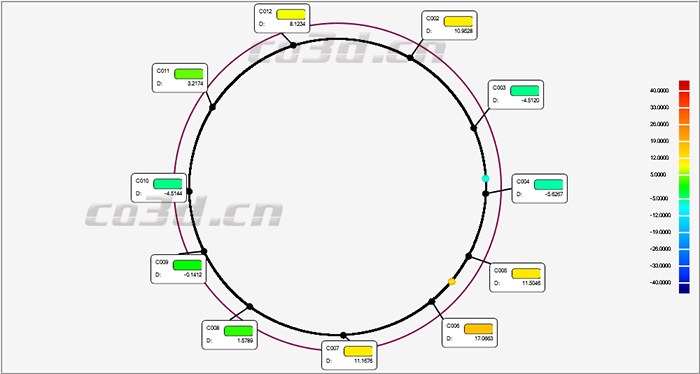
Cross section analysis of super large forging parts