Three-dimensional inspection of wind blades
The design of the blades in a wind turbine can directly affect the efficiency of wind energy conversion. Good design, reliable quality and superior performance are the decisive factors to ensure the normal and stable operation of the unit. It directly affects its annual power generation and is an important part of wind energy utilization. 3D scanning technology is used to quickly obtain 3D data of the inspection position of the blade, and through data analysis and comparison, we can understand the existence of the problem and make timely maintenance to ensure the operation of the work.
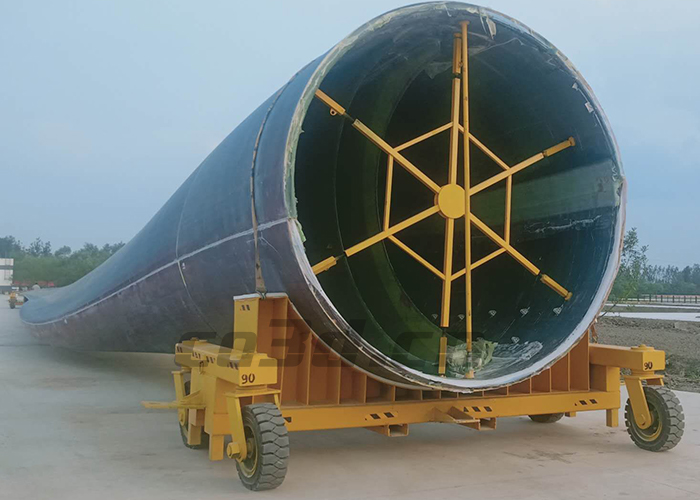
Site scan
Practical problems
The customer needs to check the size of the outer ring of the blade root to check the amount of deformation. And it requires high precision, fast scanning speed, and can complete the work efficiently. Due to the large size of the blade (80 meters long,More than 3 meters in diameter), it is inconvenient to move, relying on manual traditional measurement methods, the efficiency is low, the accuracy is not up to the requirements, and accurate detection cannot be performed. Therefore, three-dimensional scanning detection is adopted.
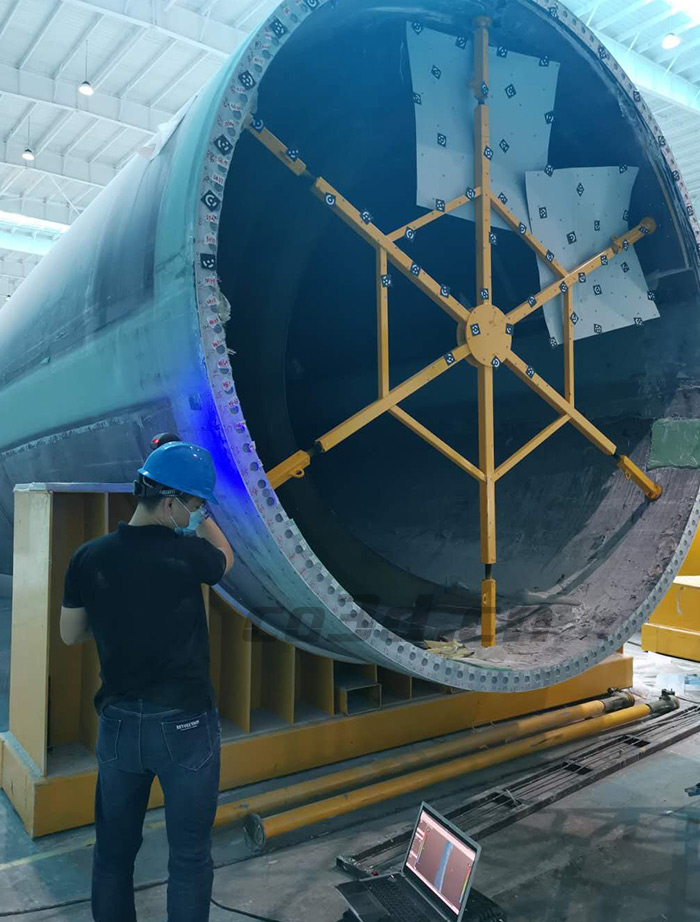
Site scan
Co3d solution
According to customer needs and workpiece conditions, Co3d technical engineers use 3D photogrammetry HL-3DP with the handheld 3D scanner HOLON751 to scan to obtain data, which can reduce the cumulative error of 3D scanning data splicing.
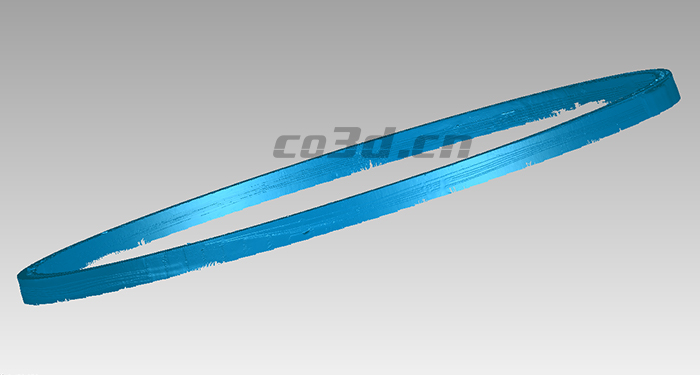
Scan STL data graph
First, use the three-dimensional photogrammetry HL-3DP to obtain the 3D coordinates of the inspection site. Then use the handheld 3D scanner HOLON751 to scan to obtain high-precision data with fast scanning speed and efficient completion of the work. Import the data into the 3D inspection software for comparison and analysis with the original digital model, and export the data analysis report to know the amount of deformation.
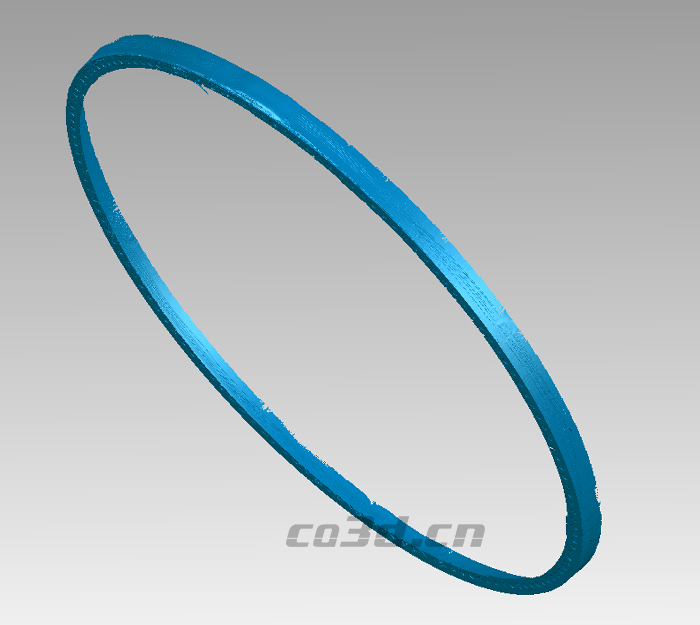
Scan STL data graph