Water turbine bucket defect detection
Most of the impulse turbines that have been operated for many years have cracks in their buckets, and some will also have bucket dropping, which has seriously affected the safety and economic operation of the hydropower station. However, most of the bucket repairs are conducted on site, the treatment process is rough, and the quality is not guaranteed, which brings hidden dangers to the operation of the unit after maintenance.
The personnel of the project team decided to use the hand-held 3D scanner to carry out all-round defect detection on the hydraulic turbine bucket
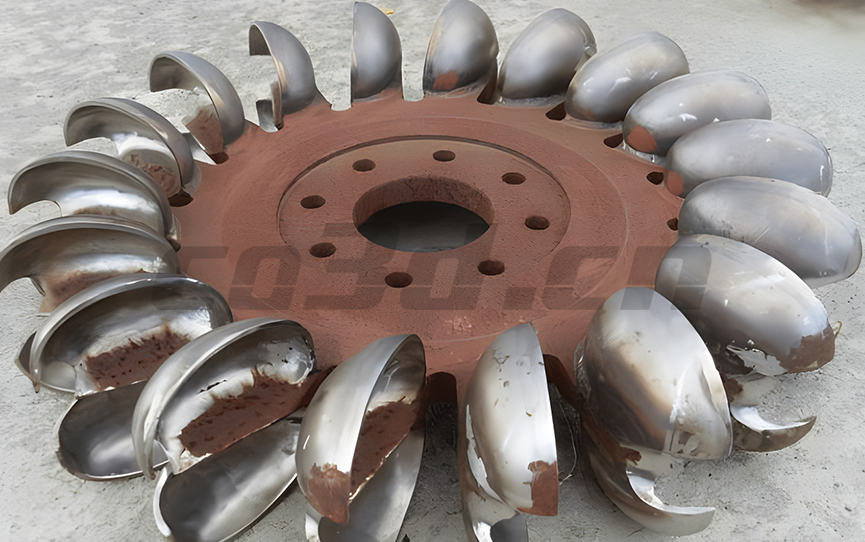
Physical drawing of water turbine bucket
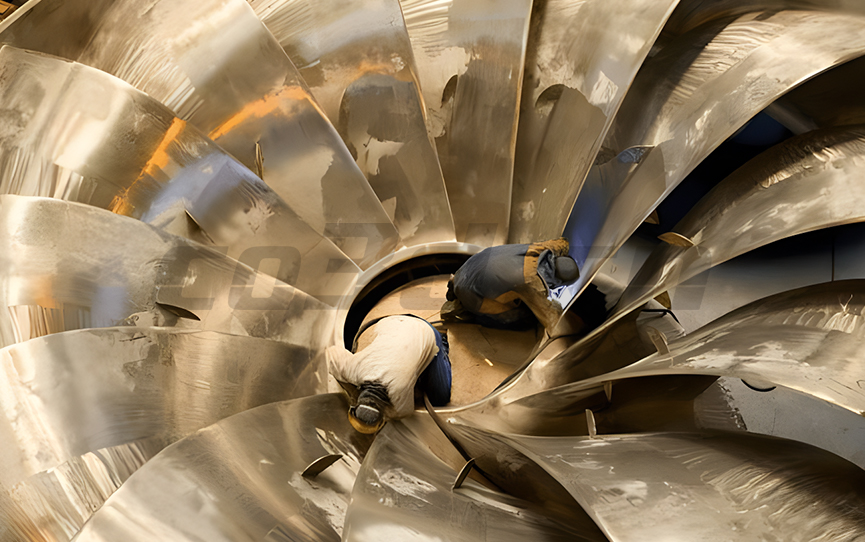
Physical drawing of water turbine bucket
Practical problem
Fine cracks on the surface of water turbine bucket during long-term forced operation
Water turbine is easy to form scale when operating in water for a long time, which has a great impact on the measured data
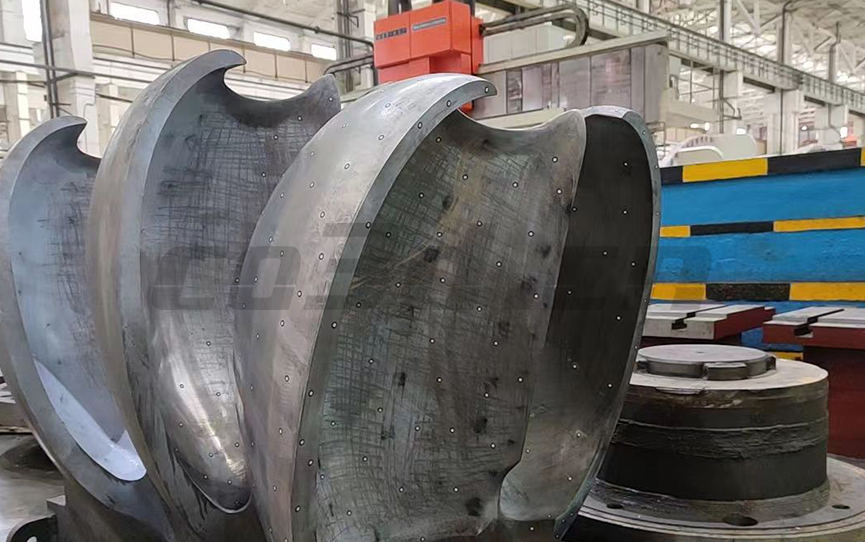
Site scanning diagram of water turbine bucket
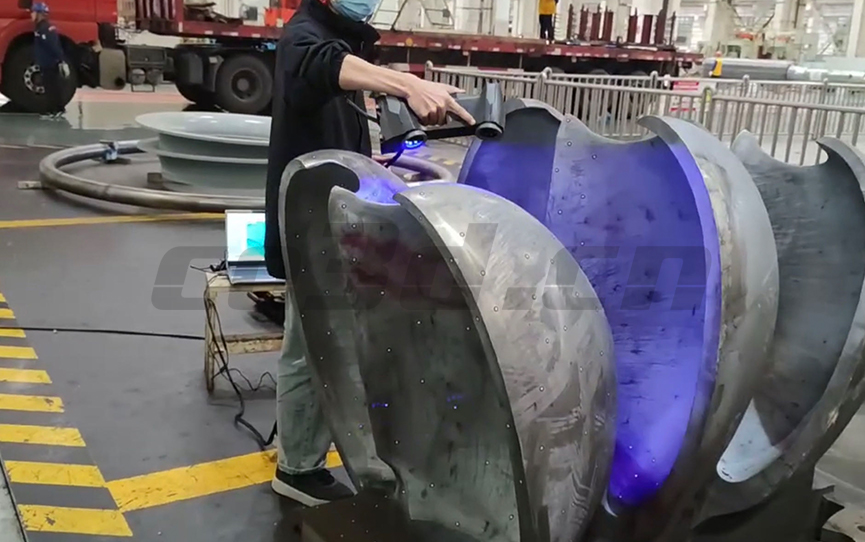
Site scanning diagram of water turbine bucket
Solutions
Advantages of using hand-held 3D scanner
·Multi-line blue light laser scanning, high-precision data scanning, can reduce the surface defect features of the bucket 1 to 1 on the crack scanning with only a minute difference on the surface
·Fast scanning, powerful single-frame data capture capability, and obvious advantages in medium and large workpiece scanning
·Strong data operation ability and intelligent matching optimal algorithm greatly reduce the accumulated error of surface 3D data.
The measurement of hydraulic turbine bucket using hand-held 3D scanning can effectively reduce the maintenance time of hydraulic turbine bucket, provide safety guarantee for the operation of the unit after maintenance, and lay a solid foundation for the long-term safe operation of follow-up hydraulic power generation.
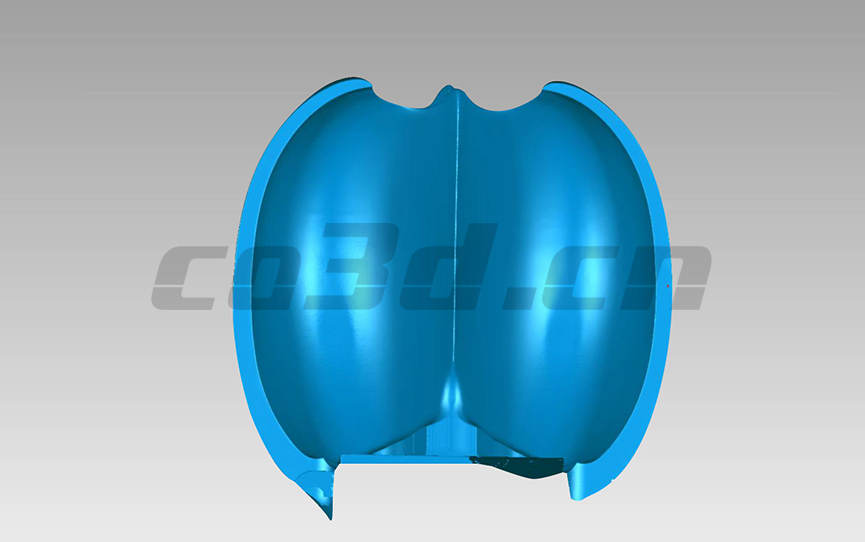
STL data diagram of turbine bucket
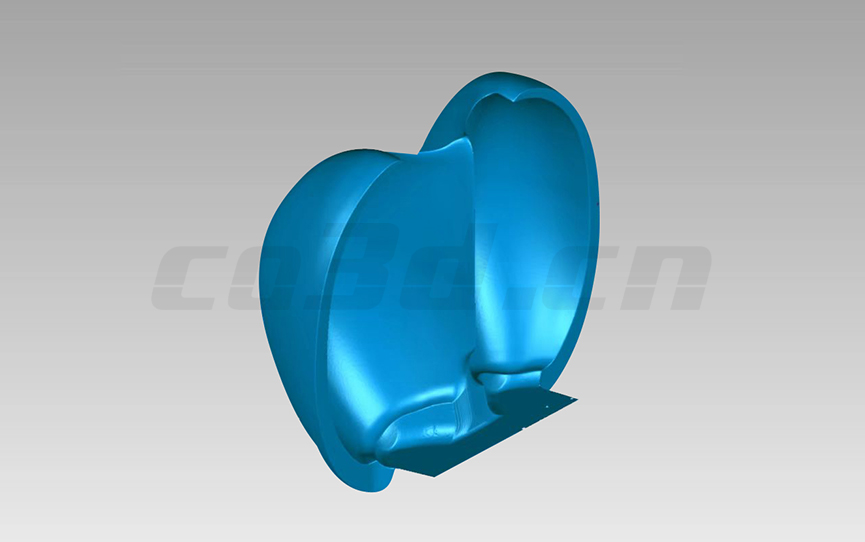
STL data diagram of turbine bucket