Three-dimensional reverse design of blast furnace chute
During the working process of the blast furnace, the charge flows from the material flow regulating valve to the distribution chute through a high drop, and is distributed to various positions of the furnace throat through the interference of the chute. The chute is prone to wear during the production process. Since the customer does not have a design drawing and cannot be repaired later, the 3D scanning technology is used to help obtain the surface data of the object, so that the reverse design can provide effective data assistance for repair and maintenance of wear.

Scanned pictures of the chute
Practical problems
The chute has a large volume and a complex structure. It scans the required parts according to customer requirements. The details also need to be scanned accurately. The data can be obtained by rapid scanning. The scanning data has high accuracy and can be used for later reverse design. Using a general 3D scanner, the scan data is incomplete, and the data cannot be scanned in subtle areas. New 3D scanning technology is required to complete the scan.
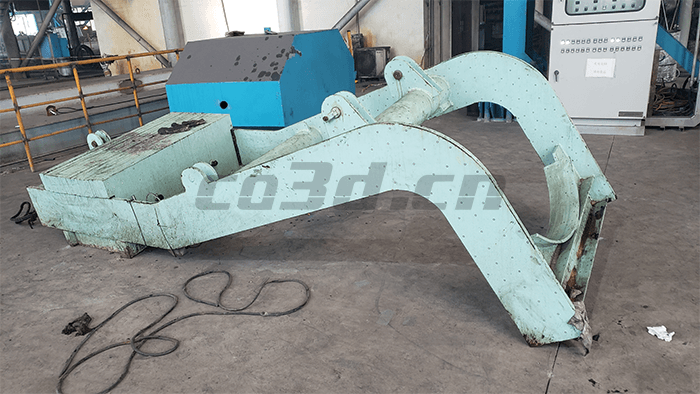
Scanned pictures of the chute
Holon solution
Using our handheld 3D scanner HOLON751, this device has a scanning accuracy of up to 0.02mm, fast scanning speed, and fine mode scanning details, easy to use, simple to operate, and can quickly complete the scanning work.
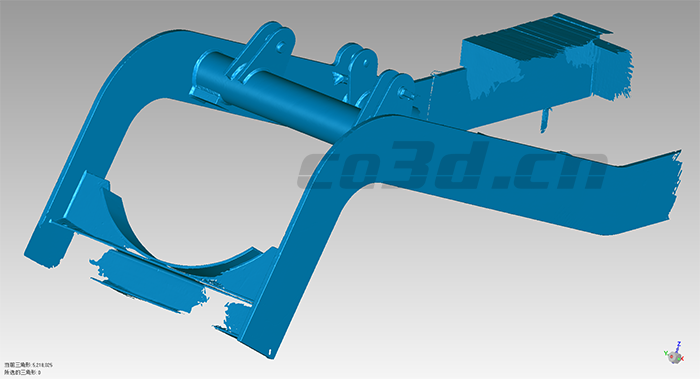
Scan STL data
First, mark points are attached for positioning and splicing, and then a three-dimensional scanner is used to scan the scanned part in all directions to obtain high-precision data. The scanning can be completed in half an hour, and the work efficiency is high. Import the scanned data into the reverse software for processing, generate a model, which can be innovatively designed, modified later, and further design more suitable products on the existing basis, helping customers solve a major problem.
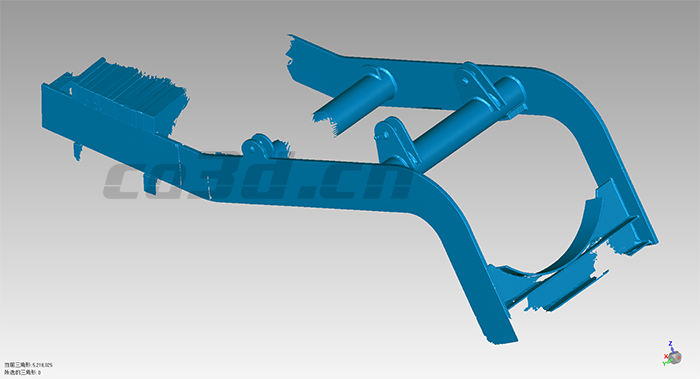
Scan STL data
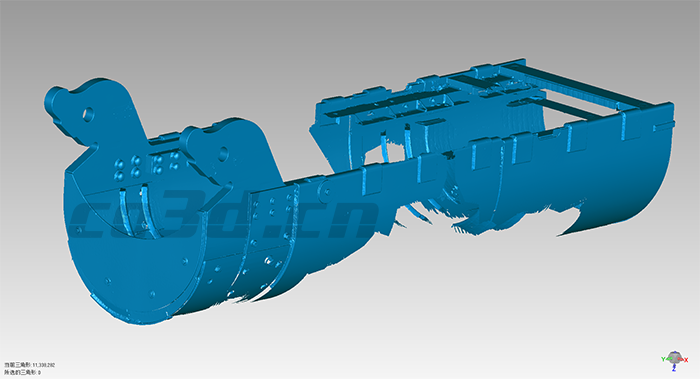
Scan STL data